Resource Articles
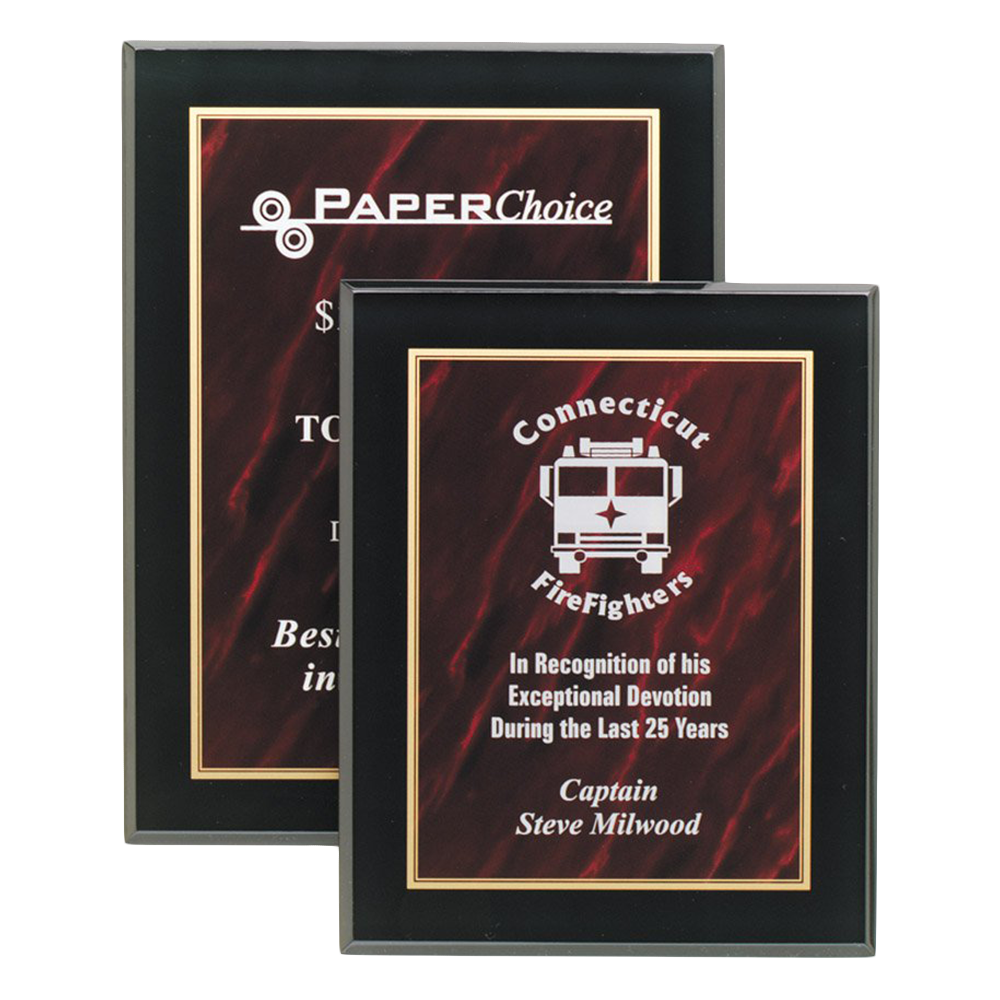
Custom Trophies: Symbols of Appreciation Corporate awards, such as custom trophies, are significant in recognizing exceptional performance. These tangible symbols of appreciation are lasting reminders of employees' accomplishments and contributions. Engraving custom trophies adds a personal touch and enhances their value as meaningful keepsakes. Organizations can create a sense of pride and commemorate individual success by customizing awards with employee names, achievement details, and company logos. The Benefits of Engraving Custom Trophies Engraving custom trophies offers several benefits that contribute to a positive work environment and foster a sense of appreciation. Some key benefits include: Personalization and Individualization Engraving allows for personalization and individualization of trophies. Custom trophies become unique and special by including the recipient's name, the specific achievement, and the date of recognition. This personal touch reinforces the award's significance and makes it more meaningful to the recipient. Long-Lasting Reminders Engraved custom trophies serve as long-lasting reminders of accomplishments. Unlike other forms of recognition, awards can be displayed prominently in the workplace or at home as a source of inspiration and motivation. They act as a visual representation of success and can boost confidence and morale. Recognition of Milestones and Achievements Engraving custom trophies allows organizations to recognize specific milestones and achievements. Whether reaching sales targets, completing a project, or demonstrating exceptional leadership, awards can be tailored to highlight these accomplishments. This recognition encourages employees to strive for excellence and sets a benchmark for future success. Showcase Company Values and Culture Custom trophies can be designed to reflect the company's values and culture. By incorporating company logos and branding elements, awards represent the organization's identity. This alignment reinforces the importance of the company's values and culture, creating a sense of pride and unity among employees. Best Practices for Engraving Custom Trophies It is essential to follow certain best practices to help organizations maximize the impact of recognition efforts and create a culture of appreciation. Here are some critical best practices to consider: Thoughtful Design and Material Selection When selecting custom trophies, consider the design and material that best aligns with the recognized achievements. The design should be visually appealing and representative of the significance of the award. Additionally, choosing high-quality materials ensures that the trophy will withstand the test of time and maintain its value. Clear and Concise Engraving The engraving on custom trophies should be clear, concise, and easily readable. Use a legible font and size, and ensure that the text stands out against the background. Include relevant details such as the recipient's name, the achievement, and the date of recognition. Avoid overcrowding the engraving space to maintain a clean and professional look. Consistency in Engraving Style Maintaining consistency in the engraving style across all custom trophies is essential. This consistency creates a cohesive and professional look, reinforcing the importance of recognition. Consider engraving templates or guidelines to ensure all awards adhere to the same style and standards. Timely Engraving and Presentation Engraving custom trophies should be done promptly to avoid delays in recognition. Once the engraving is complete, ensure the awards are presented quickly to the recipients. Timely recognition enhances the impact and shows that the organization values and appreciates the achievements of its employees. Consideration for Display and Presentation When designing custom trophies, consider how they will be displayed and presented to the recipients. Provide appropriate packaging or display cases that protect the trophies and enhance their presentation. This attention to detail adds to the overall experience of receiving the award and contributes to the sense of appreciation. Conclusion Engraving custom trophies is a powerful way to enhance appreciation and recognition in the workplace. Organizations can create lasting reminders of achievements and foster a culture of appreciation by personalizing and customizing trophies. Following best design practices for engraving ensures that awards are thoughtful, effectively communicate the achievement, and align with the company's values and culture. By implementing these practices, organizations can inspire employees, boost morale, and create a positive work environment where achievements are celebrated and recognized.
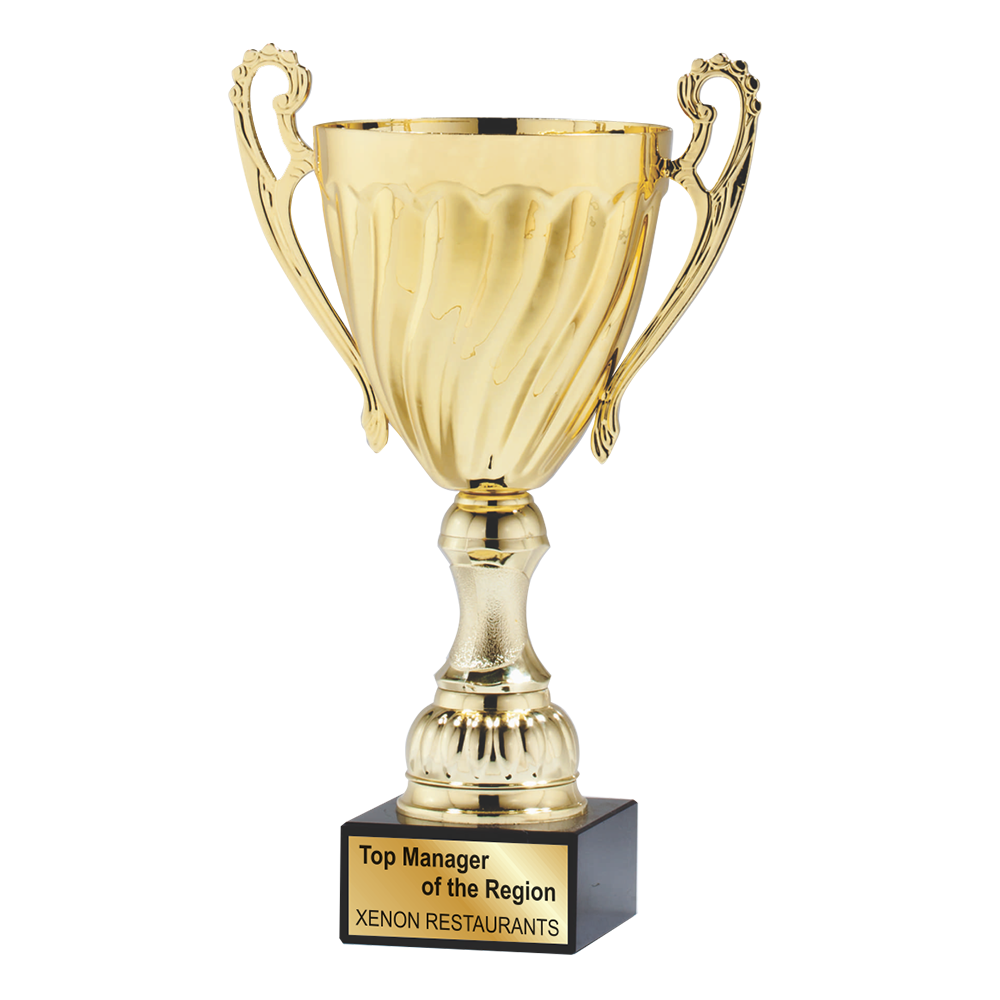
There are some traditional rules when looking for trophies and awards to celebrate success. Prizes for different places come in different colors. However, there is some leeway regarding the styles of 1st, 2nd, and 3rd place. You can choose a traditional color or one of our unique alternatives. Either way, your team will appreciate them. 1st Place For first place, gold is the standard. A gold medal shows someone has exceeded expectations and topped everyone else in their field. This bright, lustrous color stands out without being too flashy. When someone earns a gold trophy or medal, they and everyone else know they've done something right. Another standard first-place color is blue, which commonly applies to ribbons like those given at state fairs and science competitions. Alternatives A crystal award can be a great alternative to a first-place medal or ribbon. Crystal is elegant, customizable and shows that the recipient has accomplished a remarkable feat. For elegant custom trophies that stand out, a simple and stylish crystal trophy built by one of our experts could be it. 2nd Place The typical color for 2nd place trophies or medals is silver. We offer custom trophies showing a worker or team member that they did a great job, even if they didn't come in first. A silver award can be a great honor and motivator. Alternatives Look at glass trophies if you want something different than the typical 2nd place award. These custom awards are manufactured in various shades and shapes, so building an award anyone will appreciate is easy. 3rd Place A 3rd place medal or trophy is usually in bronze. It's still a precious metal but doesn't stand out like silver and gold. For ribbons, most competitors will receive one of white. In any case, 3rd place awards show that someone has done a solid job and could see impressive improvement. Alternatives Both glass trophies and crystal awards can also make for great alternatives here. Or, you can build a custom plaque that shows your appreciation for your player or employee. The wood and engraving plate are close to matching the usual bronze theme. When hung on a wall, a plaque will serve as both a source of pride and a great motivator to do even better in the future. Whether you're looking for sports trophies or corporate awards, our experts at Branded Awards are ready to deliver outstanding results.
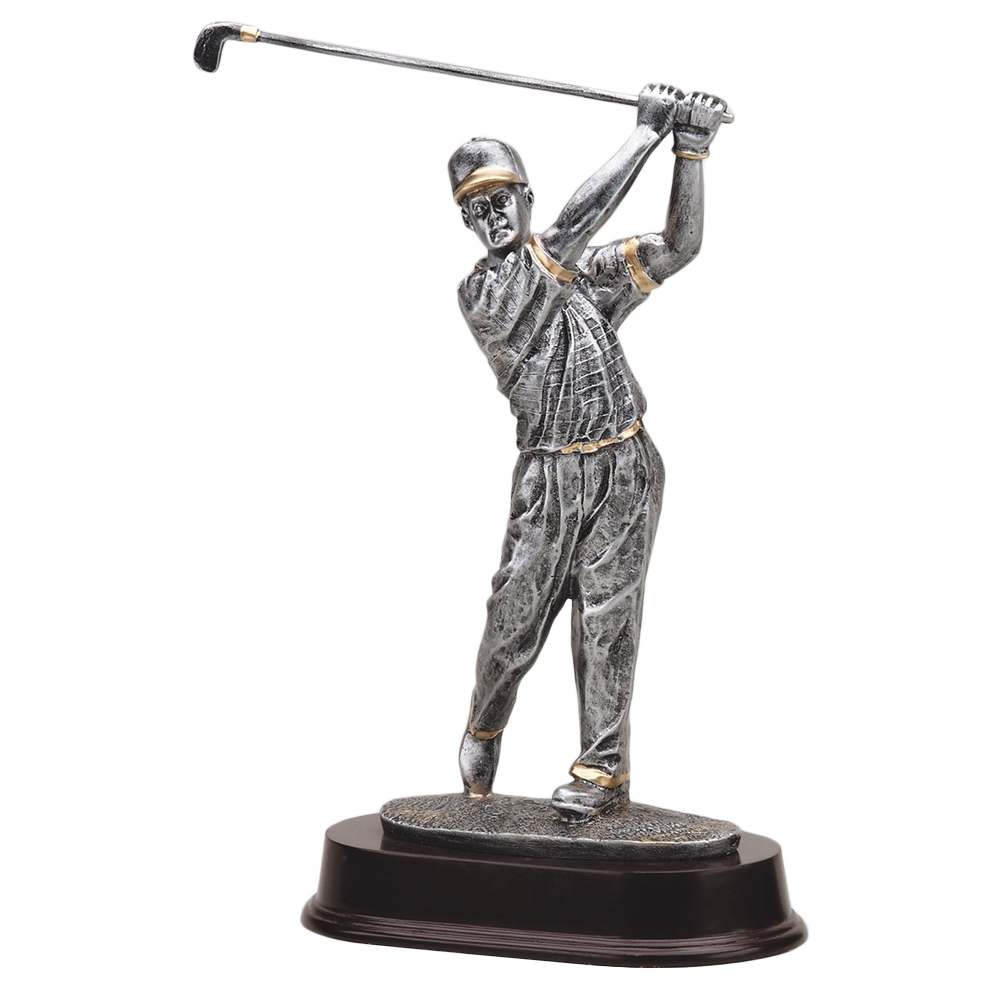
Golf tournaments, leagues, and outings are not just about the competition, but an opportunity to celebrate participants' achievements and hard work. What better way to honor their skills and dedication than by presenting them with unique and creative trophies? This guide will explore innovative trophy ideas for golf events, from personalized plaques to golf-themed awards that will make your event memorable. Personalized Plaques | A Timeless Option Plaques are a timeless way to celebrate golf's winners (and sometimes losers). With a plethora of plaque materials to choose from, make sure that you select the one that best conveys the emotion and message for your purpose. Personalized Plaques | Engraving Names in Timeless Elegance One classic option for golf awards is personalized plaques. These timeless pieces can be customized with the winners' names, making them memorable for the recipient. Depending on the desired aesthetic, plaques can be made from various materials such as wood, metal, or acrylic. Consider adding a golf-themed design or logo to enhance the overall appeal. Wooden Plaques | A Touch of Tradition Wooden plaques exude a sense of tradition and elegance. They can be crafted from high-quality woods like mahogany or oak, providing a rich and luxurious look. Engrave the champion's name, outing details, and any other relevant information on the plaque. You can also incorporate a golf club or ball design to add a unique touch. Metal Plaques | Modern and Sophisticated For a sleek and modern look, metal plaques are an excellent choice. Aluminum, brass, or stainless steel can be used to create these awards. Engrave the winners' names and tournament details on the metal surface for a sophisticated touch. Consider adding a golf-related design, such as a golf club or ball, to make the plaque genuinely representative of the sport. Acrylic Plaques | Contemporary and Versatile Acrylic plaques offer a contemporary and versatile option for golf tournament trophies. These lightweight trophies can be customized with vibrant colors, making them visually appealing. Laser engraving can etch the winner's name, event details, and other designs onto the plaque. Consider incorporating a golf-themed backdrop or a 3D golf ball for added effect. Golf-Themed Trophies | Teeing Up Creativity If you want to go beyond traditional plaques, golf-themed trophies can add a fun and unique element to your golf events. These designs can resemble golf-related objects or showcase golfing poses, making them truly representative of the sport. Let's explore some creative ideas to inspire you. Golf Club Trophies | Swinging to Victory One creative trophy idea is to design trophies in the shape of golf clubs. These can be made from various materials, such as metal or resin, and customized to match the winners' clubs. Consider incorporating details such as names, tournament details, and event year. These trophies celebrate the champions and symbolize their dedication to the sport. Golf Ball Trophies | A Hole-in-One Celebration Another innovative trophy idea is to create awards in the shape of golf balls. These can be made from materials like crystal or resin, giving them a realistic look: Engrave names, event details, and other relevant information onto the award. Consider adding a small pedestal or base to make the golf ball more visually appealing. Golf Pose Trophies | Capturing the Perfect Swing Consider creating trophies depicting various golf poses for a more dynamic and artistic design. These can be made from resin or metal and showcase golfers in different swing stages. Ensure the awards are customized with the winners' names and tournament details to make them truly personalized. This design not only celebrates the champions' achievements but also captures the essence of the sport. Trophy Accessories | Adding a Touch of Customization To further personalize the golf event experience, consider adding accessories that reflect the achievements and the event's theme. These accessories can range from small details to more significant components, adding an extra layer of memories to the experience. Golf Bag Tags | Personalized Mementos Golf bag tags make for excellent accessories for participants. Customize these tags with participants' names, outing details, and any relevant designs. Consider incorporating the tournament logo or a golf-related motif to enhance the visual appeal. Golf bag tags are practical and serve as lasting mementos. Trophy Bases | Showcasing the Champions Trophy bases are an essential component of any design. They not only provide stability but also offer an opportunity to incorporate additional customization. Consider adding engraved plates to the bases, displaying names, details, and other relevant information. The trophy bases can be made from wood, marble, or acrylic, depending on the desired look and feel. Golf Ball Display Cases | Preserving the Memory Golf ball display cases are a unique and practical accessory for awards. Customize cases with the winners' names, event details, and other designs. Consider adding a clear acrylic or glass cover to protect the golf ball and allow for easy display. Golf ball display cases preserve memories and serve as conversation pieces. Celebrate Achievements on the Green By presenting fellow golfers with unique and creative awards, you can make their time on the course even more memorable. From personalized plaques to golf-themed trophies, there are endless possibilities to honor the winners and showcase their success. Let your creativity shine, and create awards that genuinely capture the spirit of the game.
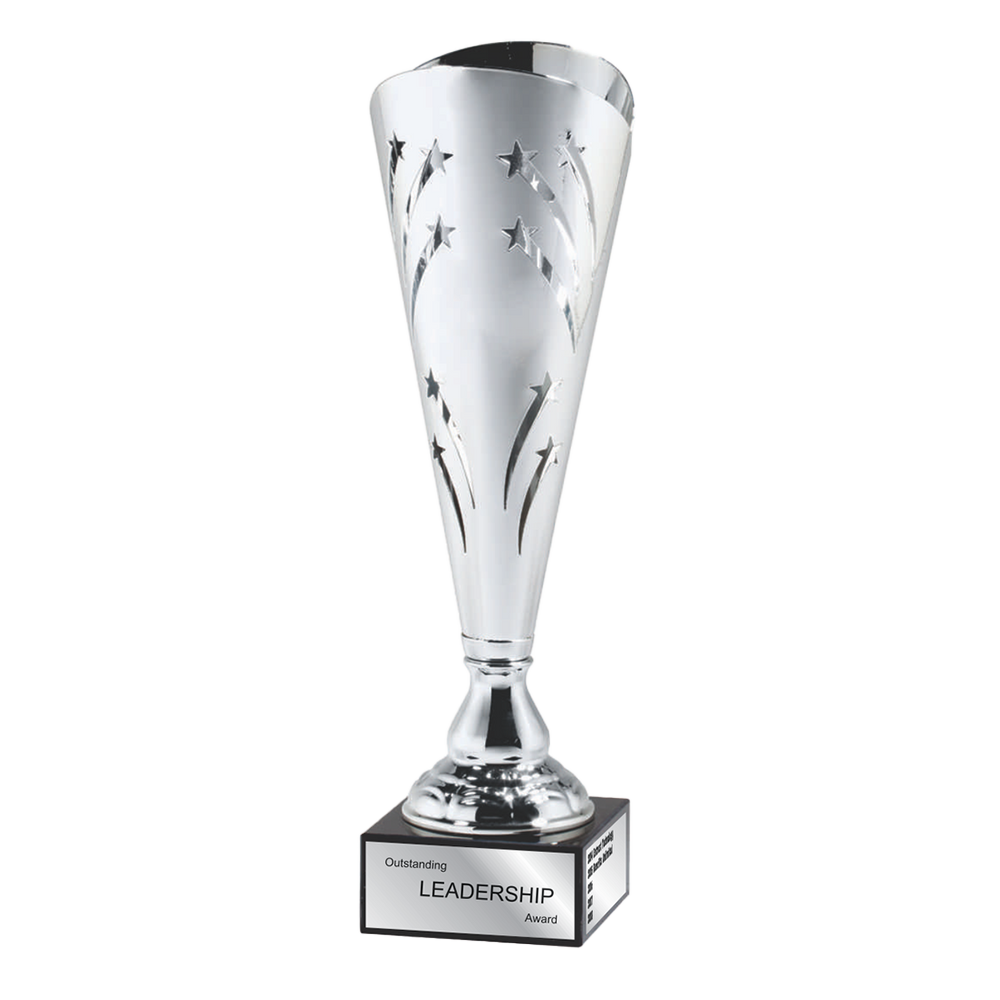
When recognizing employee achievements, custom awards play a significant role in showing appreciation and boosting employee morale. Whether it's a plaque, trophy, or certificate, a well-designed and personalized award can leave a lasting impact on recipients. However, choosing the right custom award can be a daunting task, considering the variety of options available in the market. To help you make an informed decision, we have compiled a list of the top five questions to ask when purchasing custom awards. 1. What is the Purpose of the Award? Before diving into the specifics of the award, it's essential to understand its purpose. Are you recognizing outstanding sales performance, employee tenure, or team collaboration? By identifying the purpose, you can tailor the design and message of the award to align with the recognized achievement. For example, a sales award may have a design that reflects success and growth, while a team collaboration award could focus on unity and teamwork. Consider the values and culture of your organization when determining the purpose of the award. The award should reinforce and promote these values, creating a sense of pride within the company. 2. What Material and Design Options are Available? The material and design of the award can significantly impact its overall appeal and significance. When choosing a material, consider durability, aesthetics, and budget. Common materials for custom awards include crystal, acrylic, glass, and metal. Each material has unique characteristics and can be customized to suit your requirements. In terms of design options, there are endless possibilities. From traditional plaques to modern sculptures, the design should reflect the achievement and resonate with the recipient. Consider incorporating elements such as the company logo, employee name, and a personalized message to add a personal touch to the award. 3. Can the Award be Customized? Personalization is vital when it comes to custom awards. The ability to customize the award allows you to create a unique and meaningful recognition experience for the recipient. Ask if customization options are offered, such as engravings, color printings, or custom shapes. Personalizing the award with the recipient's name, the date, and a personalized message adds a personal touch and makes the prize more memorable. Additionally, consider if the provider offers options to include the company logo or specific branding elements. Customizing the award with these elements can reinforce the connection between the recipient and the organization. 4. What is the Turnaround Time and Cost? Time and cost are important factors to consider when purchasing custom awards. Inquire about the turnaround time for production and delivery. Ensure the provider can meet your desired timeline, especially if you have a specific event or deadline. Discuss the cost of the awards and any additional fees that may apply, such as customization or shipping charges. It's essential to clearly understand the pricing structure and any potential hidden costs before deciding. 5. Can You Provide References or Samples? To ensure the quality and reliability of the award provider, ask for references or samples of their previous work, giving you a better idea of the provider's craftsmanship, attention to detail, and overall customer satisfaction. Requesting references from other satisfied customers can help you make an informed decision and gain confidence in the provider's ability to deliver high-quality custom awards. Additionally, asking for samples allows you to see and feel the quality of the awards, helping you assess the craftsmanship, materials, and overall design aesthetics. Moving Forward Purchasing custom awards requires careful consideration and attention to detail. By asking the right questions and considering factors such as the purpose, material, and design options, customization capabilities, turnaround time, and cost, you can ensure that the awards you choose are visually appealing, meaningful, impactful. Remember to prioritize quality, personalization, and alignment with your organization's values to create a recognition experience that resonates with the recipients and inspires others to achieve greatness.
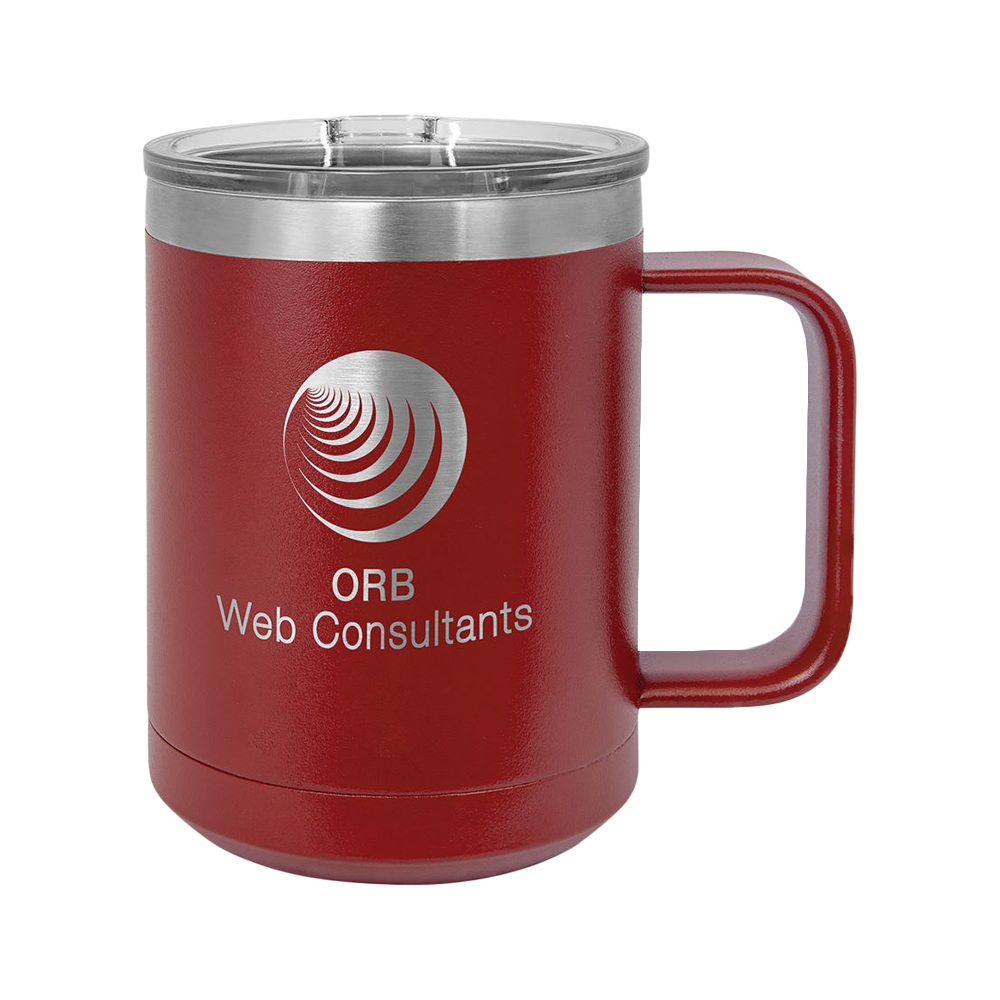
When creating custom awards, designs that align with your organization's identity and values is crucial. Here are some key factors to consider: Material Selection Choose high-quality materials that reflect the prestige and significance of the award. Consider materials such as crystal, glass, metal, or acrylic, depending on the desired aesthetic and durability. Design Elements Incorporate design elements representing your company's brand and values, including logos, symbols, or specific shapes that hold meaning for your organization. Customization Options Offer customization options that allow recipients to personalize their awards, including engraving their name, the date, or a personalized message. Unique and Creative Designs Create designs that are visually striking and unique. Consider using innovative shapes, color combinations, or artistic elements to make your custom trophies stand out. Sustainability Considerations Incorporate sustainable practices into your trophy design process. Use eco-friendly materials and explore options for recyclability or reusability. Employee recognition is a powerful tool that fosters employee motivation, loyalty, and productivity. By implementing effective recognition programs and designing custom trophies that align with your organization's identity, you can create a culture of appreciation that inspires your workforce to perform at their best.
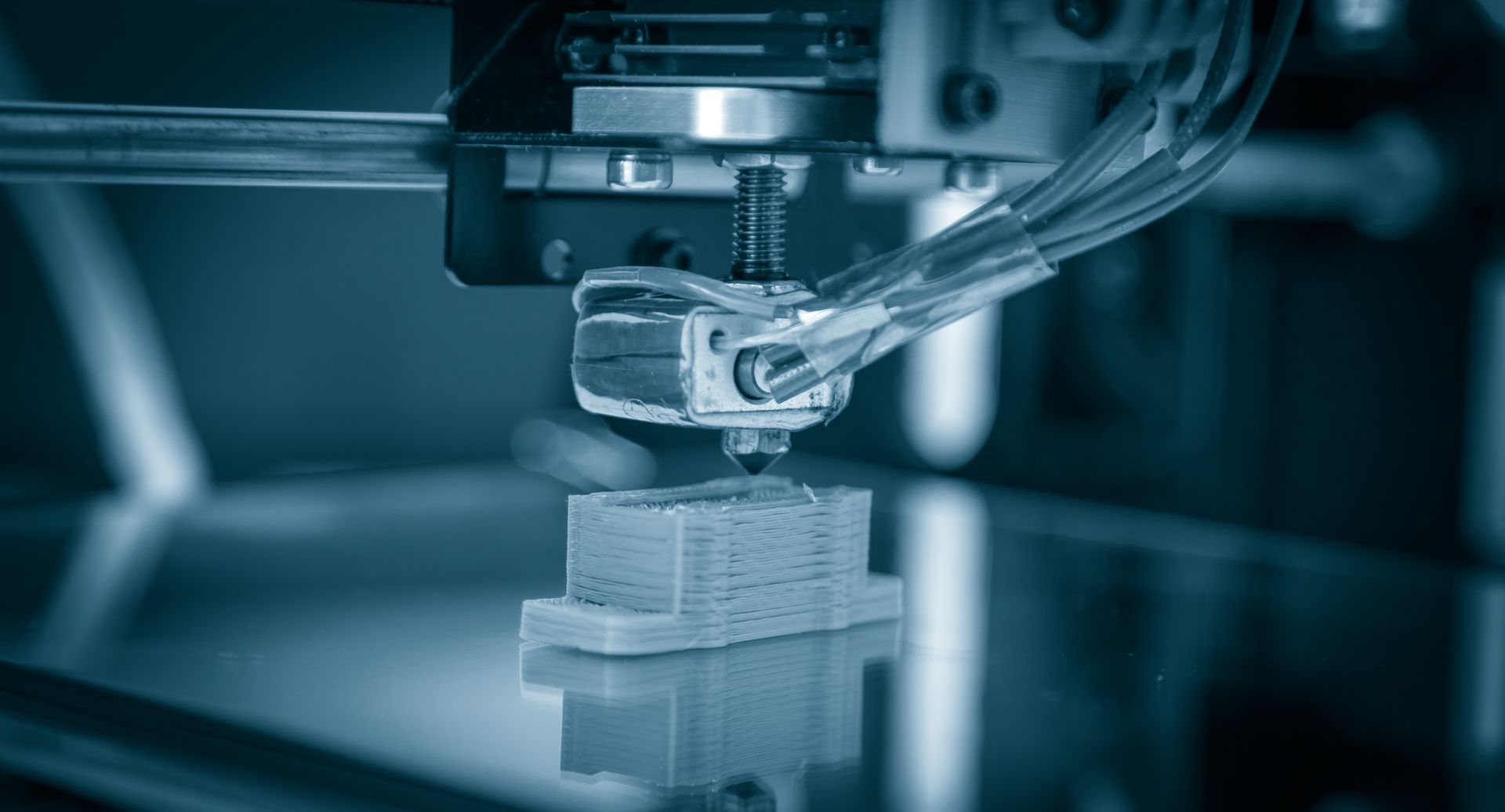
In employee recognition, trophies and awards play a significant role in acknowledging exceptional performance. Traditionally, creating these trophies involved intricate craftsmanship and expensive materials. However, with the advent of 3D printing technology, the trophy business has experienced a remarkable transformation. This article will explore how 3D printing is revolutionizing the trophy industry, from the design process to the final product, as well as the benefits of 3D printing in terms of cost-effectiveness, customization, and sustainability. The Evolution of Trophy Design Traditional Methods In the past, trophy design relied heavily on traditional manufacturing methods such as casting, molding, and engraving. Skilled artisans meticulously crafted each trophy by hand, resulting in unique and intricate designs. However, this process was time-consuming, costly, and had limited customization options. Introduction of 3D Printing The emergence of 3D printing technology revolutionized trophy design by offering a more efficient and flexible approach. 3D printing, also known as additive manufacturing, allows trophies to be created layer by layer from digital 3D models. This method eliminates the need for molds or expensive tooling, making it more cost-effective and accessible for businesses of all sizes. Advantages of 3D Printing in Trophy Production Cost-Effectiveness A primary advantage of 3D printing in the trophy business is its cost-effectiveness. Traditional trophy manufacturing methods often require significant upfront costs for tooling and molds. 3D printing minimizes these expenses, producing trophies directly from digital files. This cost reduction allows businesses to allocate their budget toward creating more personalized and high-quality awards. Customization and Personalization Another significant advantage of 3D printing in the trophy industry is the ability to create highly customized and personalized designs. Traditional manufacturing methods often limit the level of customization due to the constraints of molds and tooling. With 3D printing, designers can easily tailor trophies to meet specific requirements, including unique shapes, colors, and engravings. This level of customization allows businesses to create awards that reflect the achievements and values of the recipients. Rapid Prototyping and Iteration 3D printing enables rapid prototyping and iteration, making it easier for trophy designers to refine their designs. Changing a trophy design could be time-consuming and costly with traditional manufacturing methods. However, with 3D printing, designers can quickly produce prototypes and make adjustments as needed. This iterative process ensures that the final trophy design meets the desired specifications and quality standards. Sustainability and Material Efficiency In recent years, sustainability has become a key consideration for businesses across various industries. 3D printing offers a more sustainable alternative to traditional trophy manufacturing methods. Unlike subtractive manufacturing processes that generate significant waste, 3D printing is an additive process that only uses the necessary material, reducing material waste and contributing to a more environmentally friendly manufacturing process. Implementing 3D printing in the Trophy Business Designing with CAD Software To leverage the benefits of 3D printing in the trophy business, designers use Computer-Aided Design (CAD) software to create digital 3D models. CAD software provides various tools and features that enable designers to bring their creative vision to life. These digital models serve as the foundation for the 3D printing process. Choosing the Right 3D Printing Technology Various 3D printing technologies are available for trophy production, each with unique advantages. Some standard 3D printing technologies used in the trophy industry include: Fused Deposition Modeling (FDM): FDM is a popular 3D printing technology that uses thermoplastic filaments to build the trophy layer by layer. It is cost-effective and offers a wide range of material options. Stereolithography (SLA): SLA utilizes a liquid resin that is solidified layer by layer using a UV laser. This technology produces highly detailed and smooth surfaces, making it ideal for intricate trophy designs. Selective Laser Sintering (SLS): SLS uses a laser to selectively fuse powdered materials, such as nylon, into the desired shape. This technology is known for its strength and durability, making it suitable for producing robust trophies. Post-Processing and Finishing Once the trophies are 3D printed, they often require post-processing and finishing to achieve the desired appearance and quality, including removing support structures, sanding, polishing, painting, or applying a protective coating. These post-processing steps ensure the awards are visually appealing and ready for presentation. The Future of 3D-Printed Trophies As 3D printing technology advances, the future of 3D printed awards looks promising. Here are some potential developments we may see in the coming years: Advanced Materials Researchers and manufacturers are constantly exploring new materials for 3D printing. In the future, we may see innovative materials designed explicitly for trophy production. These materials could offer unique properties such as enhanced durability, transparency, or even the incorporation of metal elements. Enhanced Design Capabilities With advancements in CAD software and 3D modeling techniques, designers will have even greater flexibility and creativity when designing trophies, including quickly incorporating intricate details, textures, and complex geometries into trophy designs. Integration of IoT and Smart Features As technology continually evolves, we may witness the integration of Internet of Things (IoT) capabilities and intelligent features into 3D-printed awards, including embedded sensors, LED lighting, or interactive elements that enhance the overall trophy experience. Changing the Industry 3D printing has undeniably revolutionized the trophy business, offering cost-effective, customizable, and sustainable solutions. With the ability to create highly personalized trophies and iterate designs rapidly, companies can now give their employees meaningful recognition that reflects their achievements. As technology advances, the future of 3D-printed trophies looks bright, promising even greater design capabilities and innovative features. Embracing 3D printing in the trophy industry is a smart business move and a way to elevate the employee recognition experience to new heights.
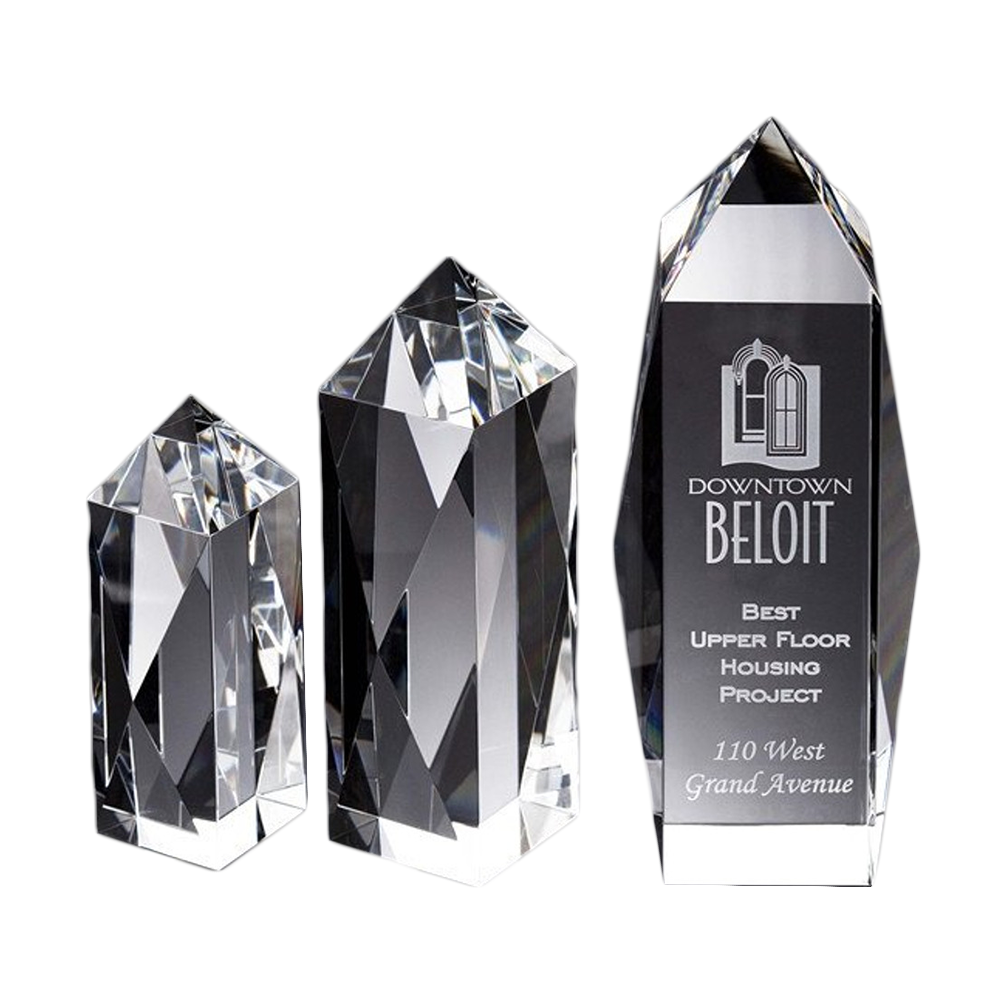
The material of an award plays a crucial role in conveying its significance and prestige. Different materials evoke different emotions and create distinct impressions. Therefore, it is essential to carefully consider the message you want to share through the choice of material. Below are three factors to remember when deciding what material to have your awards made out of. Durability and Longevity Make awards out of materials that withstand the test of time. Opting for durable materials ensures it will remain intact and visually appealing for years. Durability is essential for awards that will be displayed prominently, such as plaques or trophies. Visual Appeal The material of an award significantly impacts its visual appeal. A suitable medium enhances the overall design, making it visually stunning and aesthetically pleasing. Selecting a material that aligns with your organization's brand and the significance of the recognized achievement is crucial. Symbolic Representation The material of an award symbolizes the values and ideals of an organization. For example, glass or crystal awards may represent clarity, transparency, and excellence. On the other hand, wood awards convey a sense of natural beauty and sustainability. Consider how the material aligns with the message you want to say through the award. Consider All of the Factors While there are many other factors to consider when designing and purchasing an award, asking yourself these three questions will provide a solid base to guide you throughout the process and ensure you have a stunning prize to present.